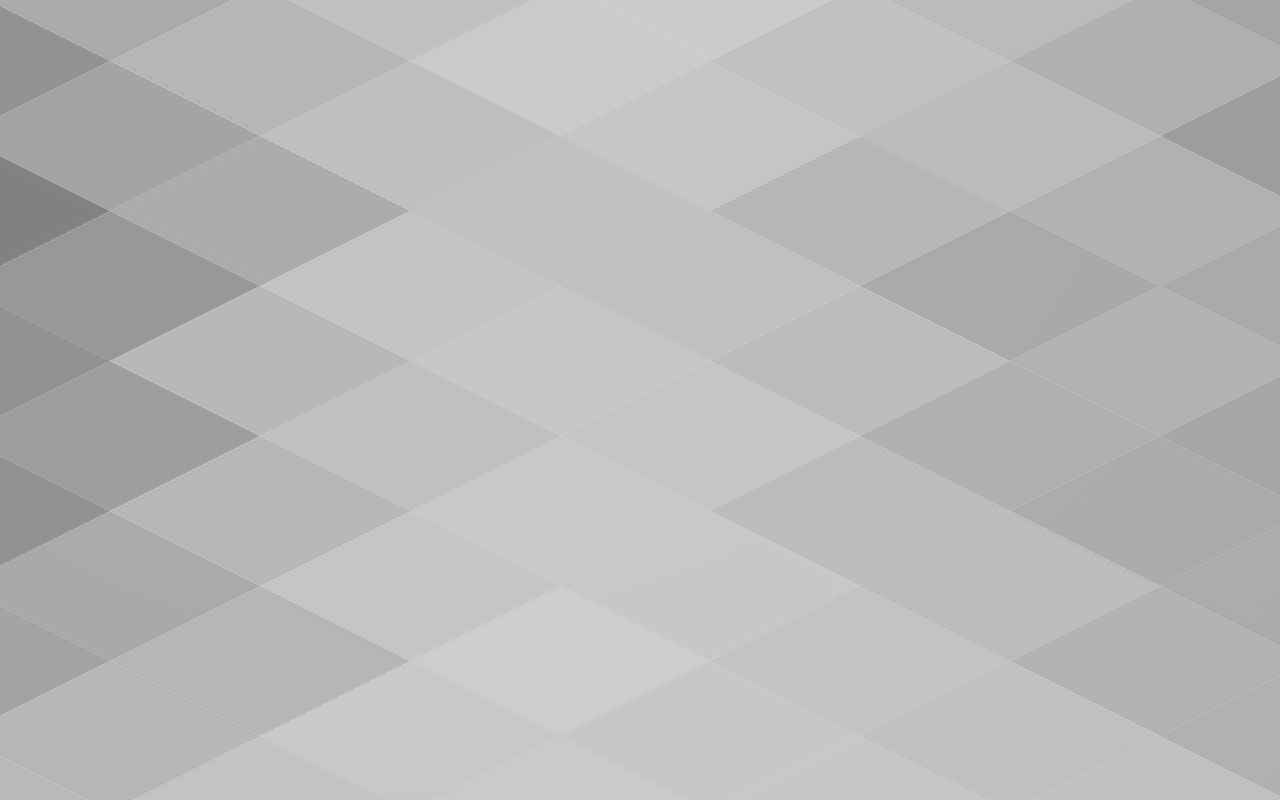
PAST COMPLETED PROJECTS
In February of 2017, I made the decision to purchase my own 3d printer - an original Prusa i3 MK2. Immediately after building the kit, I needed something to keep myself busy, and decided to design and 3d print my own low cost CNC machine. The process took a little less than two months, although the system is always being changed and enhanced.
Low-Budget CNC Router
Feb - Mar, 2017
After completing my low-budget CNC machine, I used CAD to design a paste extrusion platform for my CNC. The design incorporates the use of a syringe and lead screw to force a liquid out of various sized syringe needles. The result allowed me to 3d print materials that I previously had not been able to. Successful tests were done using chocolate icing, plumbing caulk, and drywall mud.
Paste Extrusion Effector
May, 2017
During the summer between high school and college, I became very interested in the process of vacuum forming. I decided to build my own vacuum forming table using some scrap lumber I had lying around. The end result was a functional manufacturing tool that allowed me to explore the use of formed plastic sheeting in my projects.
Vacuum Forming Table
Aug, 2016
As a senior high school physics project, I created a scale fiberglass wind tunnel. I built a mold from MDF (medium density fiberboard), which was then coated in a PVA (Poly-Vinyl Alcohol) release agent. Fiberglass cloth was laid on, cured, and then sanded and painted. To complete the project, I added a polycarbonate viewing window, an air straightener made from plastic straws, and an electric motor and propeller from a model aircraft.
I used an upholstery steamer, LED lights, and a model car to present the project and to allow visualization of the air-flow through the tunnel.
Scale Fiberglass Wind tunnel
Mar, 2016
Using the drawings provided to me in the last few images, I modeled this replica train casting using Autodesk Fusion 360. The part was later 3D printed for the customer, who intends to create a mold to cast the part in aluminum.
This is a good example of the kind of design work I often do for customers through the University of Illinois MakerLab.